How to design magnetic connectors?
The design of magnetic connectors is a complex process involving multidisciplinary knowledge, requiring comprehensive consideration of electrical performance, mechanical structure, material selection, safety, and user experience. The following is a detailed description of the
magnetic connector design process:
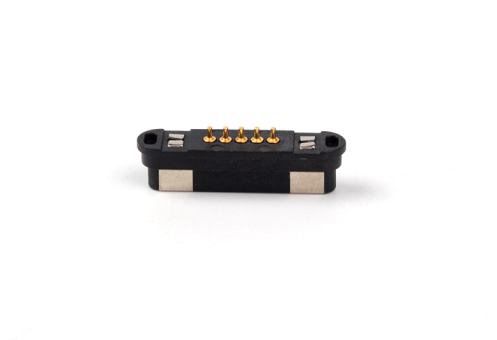
1. Demand analysis
1. Application scenario: Specify which devices or systems the magnetic connector will be applied to, such as smart phones, tablets, smart watches, smart home devices, etc. Different application scenarios may have different performance requirements for magnetic connectors.
2. Functional requirements: Determine the functions that the magnetic connector needs to achieve, such as charging, data transmission, audio transmission, etc. At the same time, you also need to consider whether you need to support advanced features such as fast charging and high-speed data transmission.
3. Performance indicators: Based on application scenarios and functional requirements, determine the performance indicators of the magnetic connector, such as contact resistance, current carrying capacity, frequency response, and plug and remove life.
Second, electrical design
1. Contact system: Design a suitable contact system to ensure that the magnetic connector can form good electrical contact when connected. The contact system usually includes conductive needle, spring, contact plate and other components. Conductive needle materials should be selected with good electrical conductivity, corrosion resistance, wear resistance of metals, such as copper, silver or alloys. The spring should be designed to provide sufficient contact force during the connection, while maintaining some elasticity in response to vibration and shock.
2. Signal transmission: For magnetic connectors that need to transmit signals, such as audio, video or data signals, a suitable signal transmission channel needs to be designed. This includes selecting the appropriate signal transmission line and designing the appropriate impedance matching network.
3. Electromagnetic compatibility: Consider the electromagnetic interference between the magnetic connector and other electronic components, and design appropriate electromagnetic shielding measures, such as the use of shielding covers, filters, etc.
Third, mechanical structure design
1. Magnetic system: Design a suitable magnetic system to ensure that the magnetic connector can be stably adsorbed together. Magnetic systems usually include permanent magnets, electromagnets or magnetic materials. The selection of permanent magnets should consider its magnetic energy product, coercive force and other parameters to ensure sufficient adsorption force. The design of the electromagnet should ensure that enough magnetic field can be generated when energized to offset the magnetic force of the permanent magnet and achieve the separation of the connector.
2. Housing and fixing mode: Design a suitable housing and fixing mode to protect the internal components of the magnetic connector and provide a stable connection. The material of the shell should be selected with a certain strength, wear resistance, corrosion resistance, such as plastic, metal or alloy. The fixing method can be threaded connection, clip connection, or adhesive connection, depending on the application scenario and requirements.
3. Insertion and withdrawal force and guide structure: Design appropriate insertion and withdrawal force and guide structure to ensure that the magnetic connector can be easily inserted and removed, and reduce wear and damage. The size of the insertion and withdrawal force should be moderate, both to ensure the stability of the connection, and to facilitate user operation. The guide structure should be designed to ensure that the connector can be guided correctly during insertion to avoid skew or damage.
Fourth, material selection
1. Conductive material: Select metal with good conductivity, corrosion resistance and wear resistance as conductive needle and contact sheet material, such as copper, silver or alloy.
2. Magnetic materials: Select permanent magnets with high magnetic energy product and strong coercivity as materials for magnetic absorption systems, such as NdFeB (NdFeB). For the electromagnet part, the appropriate coil and core material can be selected.
3. Shell material: Choose a material with certain strength, wear resistance, corrosion resistance as a shell material, such as plastic (ABS, PC, etc.), metal (aluminum, stainless steel, etc.) or alloy.
5. Security design
1. Overcurrent protection: Design a suitable overcurrent protection circuit to prevent the magnetic connector from being damaged during overload or short circuit. The overcurrent protection circuit may include elements such as a fuse, a current limiting resistor, etc.
2. Anti-misinsertion design: For the magnetic connector that needs to be prevented from misinsertion, a suitable anti-misinsertion structure can be designed, such as different plug shapes, sizes or colors.
3. Insulation design: Ensure that the various parts of the magnetic connector have sufficient insulation performance to prevent the occurrence of dangerous situations such as electrical short circuit or electric shock.
6. User experience design
1. Insertion and withdrawal feel: Design a suitable insertion and withdrawal feel, so that the magnetic connector can bring comfortable experience to the user when inserting and pulling out. The quality of inserting and pulling hand depends on factors such as the size of inserting and pulling force, the design of guiding structure and the material of the shell.
2. Appearance design: Design appearance and color matching that meet users' aesthetic needs to enhance the overall beauty and market competitiveness of the product.
3. Identification and description: Clear instructions and identification information are marked on the shell of the magnetic connector, so that users can correctly use and maintain the product.
7. Testing and verification
1. Performance test: magnetic connector performance test, including contact resistance, current carrying capacity, frequency response, plug life and other indicators of the test. Test to verify whether the magnetic connector meets the design requirements.
2. Reliability test: Reliability test for magnetic connector, including vibration test, impact test, temperature cycle test, etc. Test to verify the reliability and stability of magnetic connectors in a variety of harsh environments.
3. Safety test: Carry out safety test on magnetic connector, including overcurrent protection test, insulation resistance test, etc. Test to verify that magnetic connectors comply with relevant safety standards and regulatory requirements.
Viii. Summary
The design of magnetic connectors is a comprehensive process that requires comprehensive consideration of electrical performance, mechanical structure, material selection, safety and user experience. Through reasonable design and optimization, magnetic connector products with stable performance, safety and reliability and good user experience can be developed.